A machine breakdown could disrupt the flow of the entire operation, not just of your business but also of your customers. And the financial impact of a prolonged downtime could be significant. This is why a preventive maintenance plan (PMP) is essential to minimize sudden failures of machinery and ensure a smooth, uninterrupted workflow.
Unlike reactive maintenance, which addresses a particular faulty machine, a preventive maintenance plan ensures its regular upkeep without waiting for disruptions to emerge. And this approach has multiple long-term advantages over adopting a reactive response.
What is a preventive maintenance plan?
A preventive maintenance plan is a system to extend the lifetime of machinery and take steps to actively prevent equipment failure. Preventive maintenance work is done when there aren’t any fires to put out and creates useful information that a company can analyze to gauge when its equipment could fail in the future.
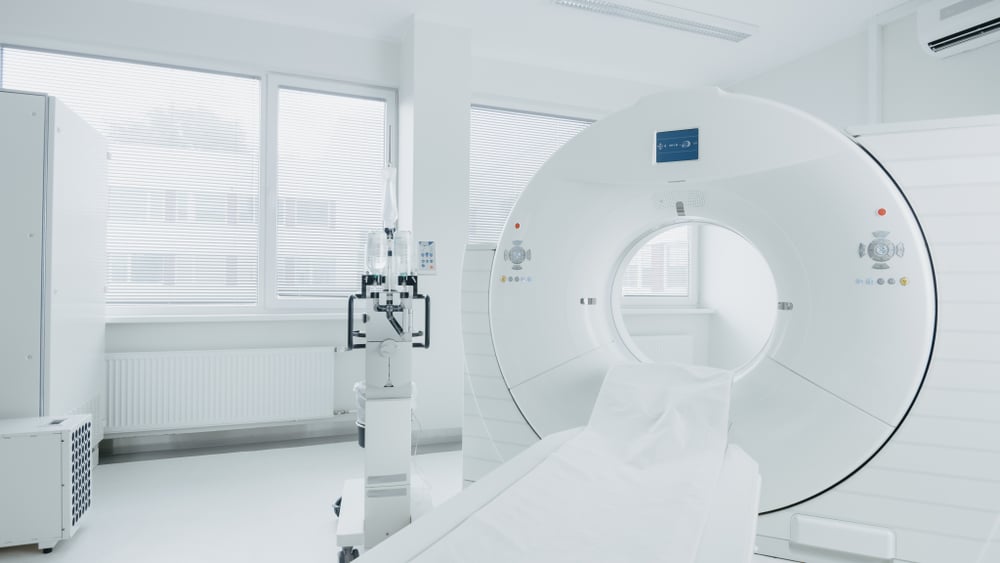
In the biomedical industry, having a preventive maintenance plan is required by the FDA.
What’s the difference between preventive maintenance and reactive maintenance?
With reactive maintenance, technicians get mobilized when a malfunction occurs. Their focus is on resolving a specific issue. Preventive maintenance, on the other hand, adopts a more holistic approach where regular maintenance is carried out regardless of the machine condition.
Why do you need a preventive maintenance plan?
A preventive maintenance plan helps minimize future breakdowns and downtime and serves to extend the useful lifetime of machinery. It allows your teams to plan their work better and maintain operational efficiency without unexpected disruptions. A PMP is also important to ensure workplace safety and is often an essential requirement for certifications and audit compliance.
Besides, the cost of attending to a malfunction with reactive maintenance has many hidden facets. It’s not just limited to the repairing expenses. The cost of downtime, product unavailability, interruptions to the sales pipeline, and even lost credibility could have a far-reaching impact on your business. And the short-term expenses of a preventive maintenance plan are often dwarfed by these unplanned long-term costs. So in the long run, preventive action will serve as a cost-effective strategy for businesses that rely on critical machinery and equipment.
What are the five elements of a successful preventive maintenance plan?
Developing a preventive maintenance plan for your organization involves five essential steps.
- Map your assets with detailed precision. Identify their business impact to determine criticality.
- Collate OEM recommendation manuals. These will guide you through the servicing requirements for optimum results.
- Get your on-ground staff involved. They will provide useful insights to make your plan practical and actionable.
- Develop the preventive maintenance plan by setting goals, preparing schedules, planning resources and assigning responsibilities with KPIs.
- Launch your plan and track progress. Evaluate effectiveness against the KPIs and make course corrections without delay.
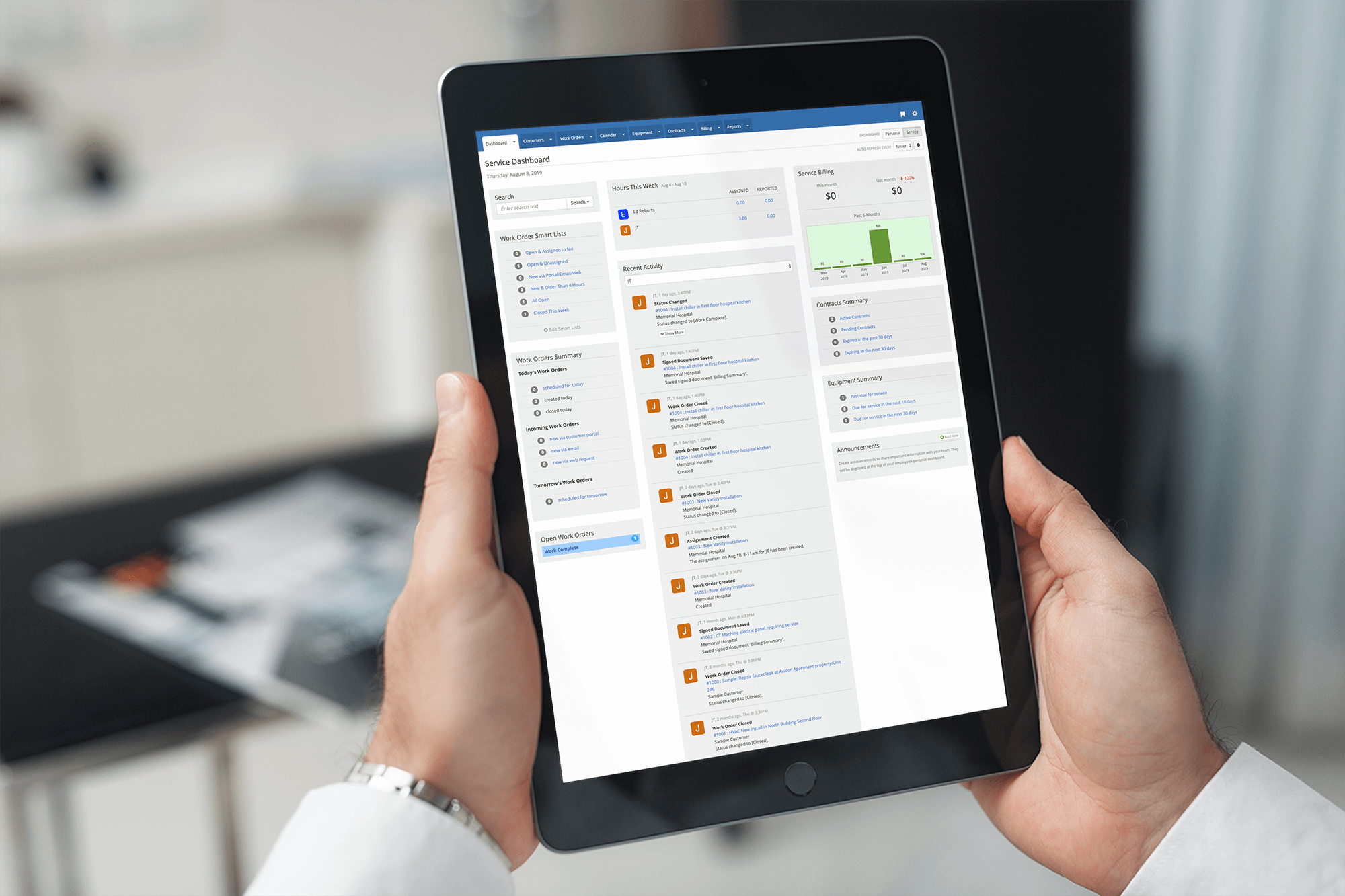
Techs can document what was done, record the overall health of the asset in question, and recommend repairs to keep everything online and functional.
1. Map Critical Assets
This inventory should be comprehensive and must cover each department. Include all important asset information such as their serial numbers, location, purchased date, recommended useful life, basic specifications, details of maintenance records, warranties and manufacturer information.
Needless to say, this is the most time-consuming step of the planning process. But it’s also the critical starting point for an effective preventive maintenance plan. So, avoid rushing and spend sufficient time to complete this stage. And continue to update this inventory as you purchase new items.
Then consider the business impact of each asset in the event of a breakdown. This risk assessment can include operational downtime, the level of disruption, cost of repairing and impact on safety and performance.
This approach enables you to prioritize and include only critical assets in your PMP by focusing on business impact as opposed to cost, size or prominence. For example, you may realize that sometimes the most critical assets are not the most expensive. And by focusing on operationally critical items, your business can develop a more efficient preventive plan and avoid wasting resources on low-impact assets.
2. Document Original Equipment Manufacturer Recommendations
These Original Equipment Manufacturer (OEM) recommendations are often prepared following extensive product testing and customer feedback. So, they are specifically developed to help prolong the useful life of your equipment, while minimizing breakdowns. So it’s the easiest way to understand the regular maintenance requirements of your critical assets to keep them in their optimum condition throughout their life cycle.
And they will make it easier for you to plan the necessary tools, financial resources and staff to carry out the required work. You can also identify when you would need the services of a third-party supplier and budget these expenses ahead of time.
Following OEM recommendations are also important to keep warranties valid and to safeguard your investments in costly assets.
Therefore, record all OEM recommendation manuals in one location to make them easily accessible. Contact the manufacturer to get copies of any missing documents and update your database.
3. Bring Your On-Ground Technical and Operational Staff Into the Conversation
From the maintenance technicians to the machine operators, these employees can be a source of useful information. They are the ones who work on-ground and understand the practical challenges, requirements and organizational dynamics that could affect the successful implementation of a PMP. So, they can provide valuable insights to customize preventive activities to fit your business environment and unique needs.
For example, different operations could use the same machine in completely different contexts. They will each have their own operating frequency, usage patterns and operators with different skill levels. So, following OEM recommendations alone will not help you plan effective preventive action.
But bringing in your on-ground teams into the PMP discussions can help you understand requirements unique to your business. For instance, they can provide insightful information about work order life cycles of reactive maintenance activities and their real on-ground impact.
And they can help you understand past servicing practices and challenges that might not be so evident when assessing the formal maintenance records. You can also identify how to optimize the preventive schedules and avoid an adverse impact on regular workflow. All these will be useful for you to develop a more realistic and actionable PMP.
These conversations can also help you identify hidden skill sets among teams. This will allow you to deploy them more effectively in your maintenance schedule and provide necessary training where there are gaps. You can also identify any hiring requirements and outsourcing needs.
4. Create Your Preventive Maintenance Plan
Create schedules and plan resources based on your PMP goals. Schedules should consider short- and long-term requirements and specify daily, weekly, monthly and annual action. They should provide detailed guidance to the technician team on maintenance activities.
KPIs are another important part of an effective preventive maintenance plan. You should set them up at the outset, discuss with the maintenance team, and regularly monitor for progress.
Needless to say, you will be working with a large amount of complex data at this stage. And manually analyzing them could be a tedious and time-consuming task. It could prevent you from taking a big picture view and can increase room for human error.
Integrating Technology
BlueFolder’s field asset management software is an excellent tool to help you streamline this process. For example, it can help you maintain all asset information in one location, saving time and improving accessibility. You can instantly retrieve critical asset data such as serial numbers and warranties without flipping through files or scrolling worksheets.
It can also simplify various other time-consuming tasks for you and your team. For example, it can help you track past maintenance records, monitor maintenance progress, create new work orders, and alert you on upcoming schedules.
All these translate into significant time savings for the scheduling, monitoring and tracking processes of your preventive maintenance plan. It can help you quickly identify areas of inefficiency, deploy resources for optimum results, minimize paperwork, and dramatically improve accuracy.
And the instant reports and customizable dashboards can help organize data into meaningful information. These can further help improve your preventive maintenance plan and support decision making with actionable data.
5. Analyze and Adjust
Therefore, reviewing it periodically is essential to identify any course corrections and respond without delay. Track progress against the set KPIs and follow up on any setbacks. Use both quantitative and qualitative information to measure effectiveness and assess the overall impact on the business. Identify what is working and what is not and evaluate the bottlenecks in implementation.
Also, ensure that you speak to the on-ground staff regularly. Get input from the technicians and closely monitor the schedules. Are there gaps in communication? Is the workload too much for the maintenance team? Is it a skill gap that’s delaying work completion? Speak to the machine operators as well to identify any repeated red flags.
The reasons for an issue may not always be so obvious in a report. Therefore, these conversations can provide you deeper insights into gaps in achieving your goals. For example, a regular breakdown of a machine could sometimes result from its unsafe handling or a workflow issue. Document the feedback for future reference and adjust the PMP to get back on track.
Regularly evaluating the progress of your preventive maintenance plan is essential to identify implementation challenges and to address them on time before issues escalate. This exercise is also important when developing your next year’s plan so you can integrate key learnings to improve it further.
How do you implement a preventive maintenance plan?
Adopting a reactive approach to looking after machinery is often prompted by worries of recurring maintenance costs and additional resource needs associated with preventive action.
But in the long term, a reactive maintenance approach could drive your costs up, sometimes with irreversible consequences. The hidden costs of downtime, operational disruptions, and lost sales, customers and credibility could all add up to your breakdown expenses.
But a preventive maintenance plan can help you avoid sudden turmoil with a regular maintenance schedule. It can help minimize downtime, optimize equipment life span, and help your teams work safely and efficiently with minimum unplanned disruptions. And an effective plan can help you keep long-term expenses low by avoiding the costly impact of an unexpected breakdown.
Watch out for common pitfalls such as communication gaps, unrealistic KPIs and prioritizing non-critical assets. These could hamper the efficiency of your preventive maintenance plan and increase costs in the long term. For example, over maintenance is one of the common mistakes that can raise the overall costs of preventive activities and lower their ROI. But closely following this five-step process can help you stay the course for optimum results.
When developing a preventive maintenance plan, it’s important to set expectations from the outset to ensure it remains realistic from the start. Quantify the business impact and don’t forget to record qualitative benefits as well.
Using Technology to Amplify Results
Developing and managing a preventive maintenance plan is of course time and resource consuming. It involves collating, evaluating, assigning and tracking a massive amount of data. And the more assets you are responsible for, the more tedious this process becomes.
But a field asset management software can help you automate this process. It allows you to store all asset data in one place. You can also retrieve, evaluate and share your PMP-related data on a single platform, access past service records, and monitor the progress of current schedules. And the customizable dashboards and real-time reports can help you keep track of the PMP and make quick adjustments where needed. Overall, these digital tools can bring phenomenal efficiencies to your business.
So, if your organization is yet to benefit from an efficient preventive maintenance plan, contact BlueFolder today to see how our field asset management software can help you.